Exploring Wood Pallet Choices: Hardwood vs. Softwood Differences
Wooden pallets are everywhere, but have you ever wondered what they're made of? Curiously, the type of wood used in pallets can have a significant impact on their strength, durability, and even their environmental footprint.
In the United States, the two most common types of wood used for pallets are southern yellow pine and oak. Southern yellow pine, a softwood, is readily available, inexpensive, and can be kiln-dried for a clean product. Oak hardwood, is prized for its strength and density, making it ideal for heavy or fragile loads.
In this article, we'll examine:
-
The differences between hardwood and softwood pallets
-
The pros and cons of using pine and oak for pallets
-
How to choose the right type of wood for your specific needs
-
The environmental impact of different pallet wood choices
So, whether you're a business owner looking to optimize your shipping process or a DIY enthusiast interested in repurposing pallets, understanding the wood behind these ubiquitous platforms is essential. Let's jump into and discover the world of pallet wood!
What Are Wood Pallets Made Of: Types of Wood Used in Pallet Manufacturing
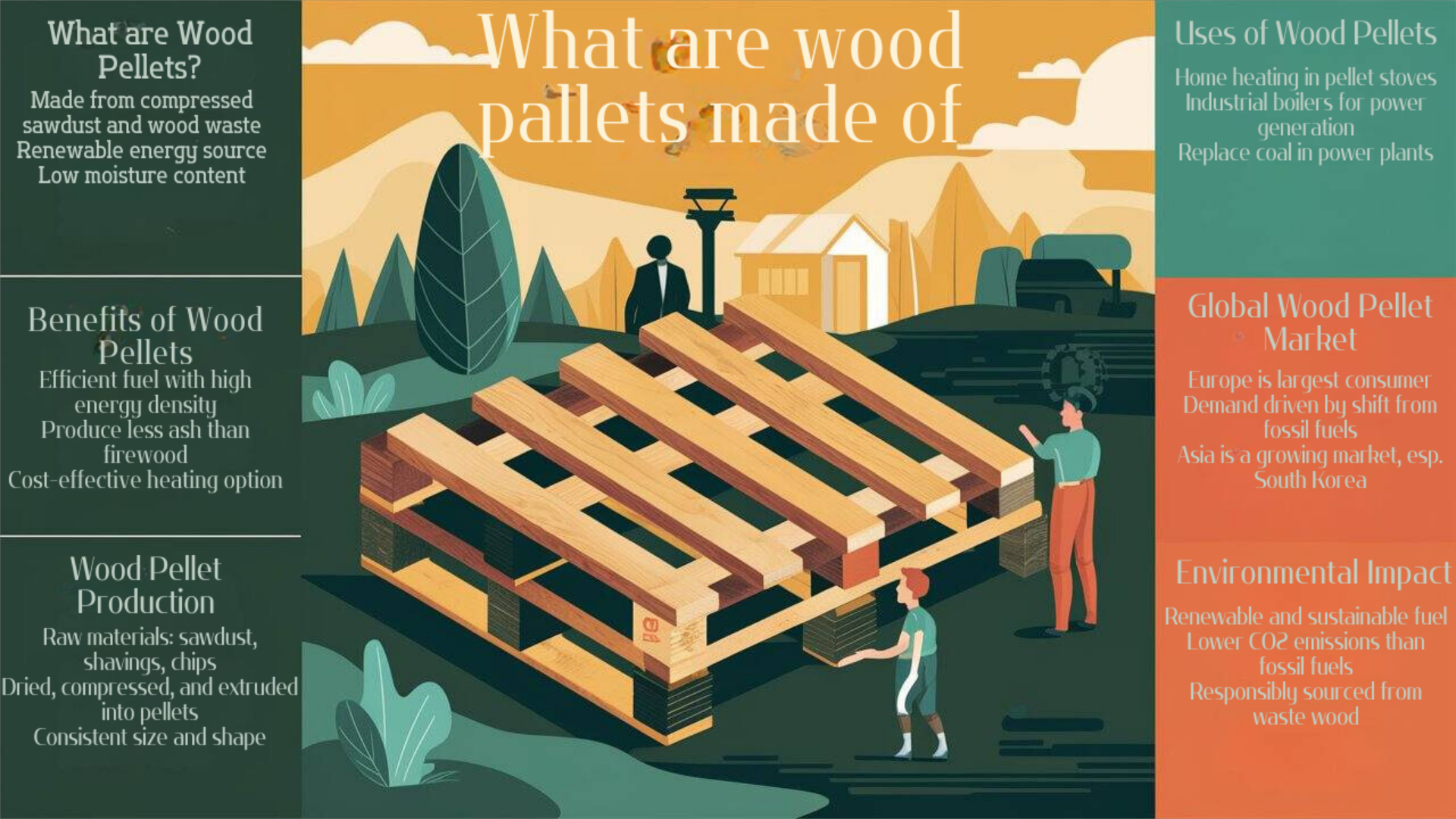
When it comes to manufacturing pallets, different types of wood are used depending on factors such as availability, cost, strength, and the need for a durable pallet. The two main categories of wood used in pallet production are hardwoods and softwoods.
Oak is a popular hardwood choice due to its strength and durability. Oak pallets are commonly used for heavy-duty applications and outdoor use.
Pine is a widely used softwood known for its cost-effectiveness and availability. Pine pallets are often chosen for shipping heavy products and are suitable for various pallet needs.
Hardwoods
Hardwoods are generally denser and more durable than softwoods, and Hardwood boards are usually 3/4” thick, making them ideal for heavy-duty applications and multiple-use pallets. Some common hardwoods used in pallet manufacturing include:
Wood Type | Characteristics |
---|---|
Oak |
- High density and strength - Resistant to wear and tear - Commonly used for heavy loads and industrial applications |
Maple |
- Fine grain, less prone to splintering - Highly resistant to shock and wear - Suitable for heavy loads and long-lasting pallets |
Birch |
- Similar properties to maple - Strong and durable - Used for heavy-duty pallets |
Other hardwoods occasionally used in pallet production include:
- Cherry
- Ash
- Beech
- Walnut
- Maple
- Poplar
Softwoods
Softwoods are generally less dense and less expensive than hardwoods. They are more readily available and easier to work with, making them a popular choice for pallet manufacturing. Common softwoods used in pallet production include:
Wood Type | Characteristics |
---|---|
Pine |
- Abundant and relatively inexpensive - Lightweight yet sturdy - Easy to work with and ideal for mass production - Commonly used for lighter loads |
Spruce |
- Lightweight properties, easy to handle - Not as durable as hardwoods - More cost-effective - Suitable for lighter loads and single-use or limited-use applications |
Fir |
- Similar properties to spruce - Lightweight and cost-effective - Suitable for lighter loads and limited-use applications |
The choice between hardwood and softwood pallets depends on various factors, such as:
- Load capacity and size
- Durability requirements
- Industry-specific regulations
- Cost considerations
- Environmental impact
By understanding the properties and characteristics of different wood types, pallet manufacturers and users can select the most suitable material for their specific needs, ensuring ideal performance and cost-effectiveness in their supply chain operations.
Pallet Manufacturing Process
The pallet manufacturing process involves several major steps to transform raw lumber into finished pallet wood ready for use. Here’s a detailed overview of the process:
Sourcing Lumber
The first step in pallet manufacturing is sourcing the appropriate lumber. Pallet manufacturers typically receive pallet cants from local sawmills, which are large pieces of wood that will be further processed.
Cutting and Shaping Components
Once the pallet cants are received, they undergo a series of cutting and shaping processes to create the individual components of the pallet:
-
Trimming: The cants are trimmed to the proper length needed for the specific pallet design.
-
Ripping: The trimmed cants are then ripped (cut lengthwise) into individual boards.
-
Sawing: The boards are sawn into the proper-sized deck boards and stringers based on the pallet specifications.
-
Notching: If required, notches are cut into the stringers to allow for 4-way entry with forklifts or 2-way entry with pallet jacks.
Heat Treatment (ISPM 15 Compliance)
If the pallets will be used for international shipping or in sanitary applications, the wood components must undergo heat treatment to comply with ISPM 15 (International Standards for Phytosanitary Measures). This process involves:
-
Heating the wood to a minimum core temperature of 56°C (132.8°F) for at least 30 minutes.
-
The treatment kills pests and reduces the moisture content of the wood, making the pallets lighter and less susceptible to contamination from fungi, molds, or other pests.
Assembly Methods
The final step in the pallet manufacturing process is assembling the components into a complete pallet. There are two primary methods for assembly:
Method | Description |
---|---|
Hand Assembly |
- Used for small orders (typically less than 200 units) - Pallets are assembled using pneumatic nailers and staplers |
Automated Assembly |
- Used for high-volume production - Machines such as board stackers, pallet nailers, and pallet stackers are used to efficiently nail together and produce pallets - Automated lines can produce up to 250 pallets per hour |
Throughout the manufacturing process, various machinery is used to maximize production and efficiency, including:
- Board stackers
- Pallet nailers
- Pallet stackers
- Robotic dismantlers
- Saws
By following these steps and utilizing the appropriate machinery, pallet manufacturers can efficiently produce high-quality wooden pallets to meet the varied needs of industries worldwide.
Hardwood vs. Softwood Pallets
When choosing between hardwood and softwood pallets, it’s necessary to understand their unique characteristics, advantages, and disadvantages, as detailed in this shipping service guide. Softwood pallets, often made from southern yellow pine, are known for their availability, cost-effectiveness, and sufficient strength for various applications. The choice, in the end, depends on your specific application, budget, and environmental considerations
Hardwood Pallets
Hardwood pallets are made from deciduous trees such as oak, maple, and hickory. They are known for their strength, durability, and resistance to wear and tear.
Advantages:
-
Durability: Hardwood pallets are more durable and can withstand heavy loads and rough handling. Oak pallets, in particular, are commonly used for heavy loads and industrial applications.
-
Moisture Resistance: Hardwood is naturally resistant to moisture, making it less susceptible to mold, bacteria, and fungal growth.
-
Long Lifespan: With proper care and maintenance, hardwood pallets can be used for multiple cycles, reducing the need for frequent replacements.
Disadvantages:
-
Cost: Hardwood pallets are generally more expensive than softwood pallets due to the slower growth rate and higher demand for hardwood lumber.
-
Weight: Hardwood pallets are heavier than softwood pallets, which can increase transportation costs and make handling more difficult.
-
Sustainability: Hardwood trees grow more slowly than softwood trees, making them less sustainable and harder to replace.
Softwood Pallets
Softwood pallets are made from coniferous trees such as pine, spruce, and fir. They are lightweight, cost-effective, and readily available.
Advantages:
-
Cost-Effective: Softwood pallets are generally less expensive than hardwood pallets due to the faster growth rate and abundance of softwood trees. Pine pallets are commonly used for lighter loads and are known for their cost-effectiveness.
-
Lightweight: Softwood pallets are lighter in mass, making them easier to handle and transport, potentially reducing shipping costs.
-
Sustainability: Softwood trees grow faster than hardwood trees, making them a more sustainable and easily replenishable resource.
Disadvantages:
-
Strength: Softwood pallets may not be as strong as hardwood pallets and may not be suitable for heavy loads or rough handling.
-
Moisture Sensitivity: Softwood is more susceptible to moisture, which can lead to warping, mold growth, and reduced structural integrity if not properly treated.
-
Shorter Lifespan: Softwood pallets may have a shorter lifespan compared to hardwood pallets, requiring more frequent replacements.
Comparison Table
Characteristic | Hardwood Pallets | Softwood Pallets |
---|---|---|
Strength | High | Moderate |
Durability | High | Moderate |
Cost | Higher | Lower |
Weight | Heavier | Lighter |
Moisture Resistance | High | Lower |
Sustainability | Lower | Higher |
Lifespan | Longer | Shorter |
At the end of the day, the choice between hardwood and softwood pallets depends on your specific requirements, budget constraints, and environmental considerations. By understanding the unique properties of each type of wood, you can make an informed decision that best suits your needs.
Recycled and Reconditioned Pallets
Recycled and reconditioned shipping pallets are cost-effective and environmentally friendly alternatives to new pallets. These pallets are retrieved, inspected, repaired, and remanufactured to extend their lifespan and reduce waste.
Benefits of Using Recycled Pallets
-
Cost Savings: Recycled pallets can be up to 70% cheaper than new pallets, depending on the grade.
-
Environmental Impact: Using recycled pallets reduces waste and supports corporate sustainability initiatives.
-
Availability: Standard-sized recycled pallets, such as 48x40 GMA pallets, are readily available in large quantities.
Reconditioning Process
The reconditioning process involves repairing and refurbishing used pallets to restore them to a usable condition. This process typically includes:
-
Inspection: Pallets are thoroughly inspected for damage and structural integrity.
-
Repair: Minor repairs are made, such as replacing, plating, or plugging deck boards and stringers.
-
Sorting: Pallets are sorted based on their condition and suitability for specific applications.
-
Quality Control: Reconditioned pallets are checked to verify they meet the required quality standards.
Quality and Safety Considerations
When using recycled or reconditioned pallets, it’s necessary to evaluate quality and safety factors:
-
Consistency: Recycled pallets may lack consistency in board thickness, fasteners, and nails placement, which can affect product palletization.
-
Failure Rate: Recycled pallets may have a higher failure rate compared to new pallets, potentially leading to product damage.
-
Mold and Contamination: Recycled pallets may be more susceptible to mold growth and contamination if not properly treated.
To guarantee the best quality and safety, work with reputable pallet recycling companies that follow to strict quality control measures and industry standards.
Pallet Recycling Services and Providers
Several companies, such as Alliance Packing, offer pallet recycling services and reconditioned pallets for sale:
Company | Services | Locations |
---|---|---|
Millwood, Inc. | Pallet recovery, recycling, and reconditioning programs | Not specified |
First Alliance Logistics Management | High-quality used wooden pallets | Across the US |
Kamps | Reconditioned and remanufactured pallets available in large wholesale quantities | Over 400 locations across the US |
Atlas Pallet | Wide variety of recycled, remanufactured, and combination pallets | RI, MA, CT, NH |
Rose Pallet | Various used and recycled wooden pallets as affordable alternatives to new pallets | Not specified |
By partnering with these pallet recycling specialists, businesses can implement cost-effective and sustainable pallet management solutions while ensuring the quality and safety of their products.
Alternative Pallet Materials
In addition to traditional wooden pallets, there are several alternative materials used in pallet manufacturing to address specific needs, such as sustainability, durability, and cost-effectiveness. Some of the most common alternative pallet materials include:
Plastic Pallets
Plastic pallets are made from various polymers, such as high-density polyethylene (HDPE) and polypropylene (PP). They offer several advantages over wooden pallets:
-
Durability: Plastic pallets are resistant to moisture, chemicals, and pests, making them suitable for long-term use and harsh environments.
-
Lightweight: Plastic pallets are generally lighter than wooden pallets, reducing shipping costs and making them easier to handle.
-
Recyclability: Most plastic pallets are recyclable, contributing to a more sustainable supply chain.
However, plastic pallets are typically more expensive than wooden pallets and may not be suitable for heavy loads.
Metal Pallets
Metal pallets, usually made from steel or aluminum, are known for their strength and durability. They are ideal for heavy-duty applications and can withstand extreme temperatures and harsh chemicals. However, metal pallets are more expensive than wooden and plastic pallets and are not as easily recyclable.
Corrugated Paper Pallets
Corrugated paper pallets are made from multiple layers of corrugated cardboard, offering a lightweight and recyclable alternative to wooden pallets[. They are:
-
Customizable: Corrugated pallets can be designed to fit specific product dimensions and requirements.
-
Recyclable: Made from paper-based materials, corrugated pallets are easily recyclable and biodegradable.
-
Lightweight: Corrugated pallets are lighter than wooden pallets, reducing shipping costs.
However, corrugated pallets may not be as durable as wooden or plastic pallets and are not suitable for outdoor storage or humid environments.
Comparison Table
Material | Strength | Durability | Cost | Weight | Recyclability |
---|---|---|---|---|---|
Wood | High | Moderate | Low | Heavy | High |
Plastic | Moderate | High | High | Light | High |
Metal | High | High | High | Heavy | Low |
Corrugated Paper | Moderate | Low | Low | Light | High |
Other alternative pallet materials include:
-
Engineered wood pallets
-
Composite pallets
-
Molded wood pallets
-
Hybrid pallets (combining different materials)
The choice of pallet material depends on various factors, such as the specific application, load requirements, environmental conditions, and budget constraints. By considering alternative pallet materials, businesses can optimize their supply chain, reduce costs, and improve sustainability.
Environmental Impact and Sustainability
The environmental impact and sustainability of a wooden pallet are primary factors to assess when evaluating their overall benefits. Wooden pallets offer several advantages regarding their renewable nature, carbon sequestration potential, and responsible forestry practices.
Renewable Nature of Wood
One of the most significant environmental benefits of wooden pallets is that they are made from a renewable resource.
-
Trees can be replanted and regrown, ensuring a continuous supply of wood for pallet production.
-
European forests, which provide a significant source of wood packaging material, have been growing by over 6,000 square kilometers annually.
-
In the United States, 1.7 billion trees are planted every year to preserve forest resources for future generations.
Recycling and Reuse of Wooden Pallets
Wooden pallets are exceptionally recyclable and reusable, contributing to their overall sustainability, as highlighted in the extensive pallet recycling services.
-
95% of wooden pallets are recovered, refurbished, and recycled or turned into another product at the end of their useful life.
-
Recycled pallets can be repaired and reused multiple times, reducing the need for new pallet production.
-
When pallets can no longer be repaired, they can be recycled into other products such as mulch, animal bedding, or biofuel.
Responsible Forestry Practices
The wood packaging industry promotes responsible forestry practices to safeguard the sustainability of forest resources.
-
Over 90% of the timber used by some pallet manufacturers comes from land certified as sustainably managed by organizations such as the Forest Stewardship Council (FSC), the Sustainable Forestry Initiative (SFI), or the American Tree Farm System (ATFS).
-
Responsible forestry practices include protecting water quality, limiting clear-cutting and deforestation, protecting high conservation value forests, and preserving wildlife habitats. as emphasized by large machinery shipping practices.
-
Modern farming and harvesting operations optimize their processes to maximize crop yields and preserve healthy, sustainable forests.
Carbon Sequestration Potential
Wood has the unique ability to store carbon, making wooden pallets a potential carbon sink.
-
Trees absorb carbon dioxide (CO2) from the atmosphere as they grow, storing carbon in their biomass.
-
The carbon remains locked within the wood, even when it is used for packaging, effectively acting as a carbon sink.
-
Each cubic meter of wood can store approximately one ton of CO2.
Environmental Benefit | Description |
---|---|
Renewable Resource | Trees can be replanted and regrown, ensuring a continuous supply of wood for pallet production, as supported by crating services. |
Recycling and Reuse | 95% of wooden pallets are recovered, refurbished, and recycled or turned into another product at the end of their useful life. |
Responsible Forestry | Over 90% of the timber used by some pallet manufacturers comes from land certified as sustainably managed. |
Carbon Sequestration | Each cubic meter of wood can store approximately one ton of CO2. |
By embracing the renewable nature of wood, promoting recycling and reuse, adhering to responsible forestry practices, and recognizing the carbon sequestration potential of wooden pallets, the wood packaging industry can meaningfully contribute to environmental sustainability and help mitigate the impacts of atmospheric change.
Industry Standards and Regulations
The wood packaging industry is subject to various standards and regulations to guarantee the safe and efficient movement of goods across international borders.. These standards and regulations aim to prevent the spread of pests and diseases while facilitating global trade.
ISPM 15 (International Standards for Phytosanitary Measures)
ISPM 15 is the most important standard for the wood packaging industry, developed by the International Plant Protection Convention (IPPC) to reduce the risk of introducing and spreading quarantine pests associated with wood packaging material.
Core requirements of ISPM 15 include:
-
Debarking: Wood packaging material must be made from debarked wood.
-
Approved Treatments: Wood must be heat-treated (HT) or fumigated with methyl bromide (MB) according to specific schedules.
-
Marking: Compliant wood packaging material must be marked with the IPPC logo, country code, producer number, and treatment type.
Treatment | Description | Minimum Requirements |
---|---|---|
Heat Treatment (HT) | Wood is heated until its core reaches a minimum temperature for a specified duration | 56°C for at least 30 minutes |
Methyl Bromide (MB) Fumigation | Wood is fumigated with methyl bromide according to a specific schedule | Dosage and duration vary based on temperature and wood thickness |
Other Relevant Standards and Regulations
In addition to ISPM 15, the wood packaging industry must comply with other standards and regulations, such as:
-
Customs Regulations: Each country has its own customs regulations for importing wood packaging material, which may include additional requirements apart from ISPM 15.
-
Environmental Regulations: Regulations related to the use of chemicals, such as methyl bromide, and the disposal of treated wood packaging material.
-
Occupational Health and Safety Regulations: Standards for ensuring the safety of workers involved in the production and handling of wood packaging material.
Compliance and Enforcement
Compliance with ISPM 15 and other relevant standards is enforced by:
-
National Plant Protection Organizations (NPPOs) in each country.
-
Customs authorities at ports of entry.
Non-compliant wood packaging material may be subject to:
-
Rejection or destruction at the port of entry.
-
Fines and penalties for the exporter or importer.
To safeguard compliance and avoid disruptions to trade, it is essential for wood packaging manufacturers, exporters, and importers to:
-
Stay informed about the latest standards and regulations.
-
Implement necessary treatments, marking, and documentation procedures.
-
Work with certified treatment providers and suppliers.
By adhering to industry standards and regulations, the wood packaging industry can support the safe and efficient global trade of goods while minimizing the environmental impact of wood packaging material.
Choosing the Right Pallet for Your Needs
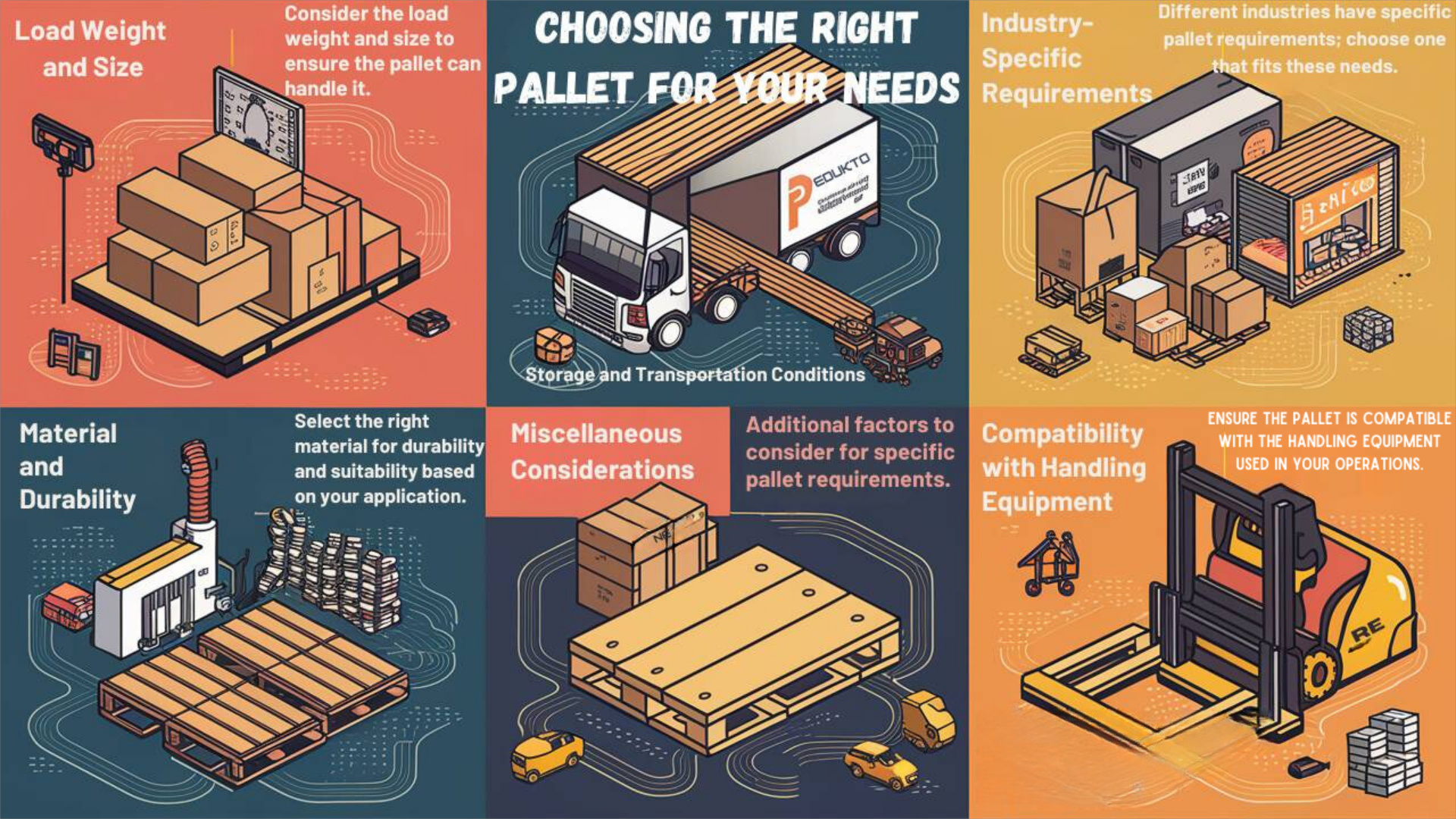
Selecting the appropriate pallet for your specific requirements is necessary to assure the safe and efficient transportation and storage of your goods. Consider the following factors when choosing the right pallet:
1. Load Capacity and Size
-
Determine the mass and dimensions of your products to confirm the pallet can support the load.
-
Choose a pallet with a sufficient load capacity to accommodate your heaviest loads.
-
Verify the pallet size is compatible with your product dimensions to prevent overhang and instability.
2. Storage and Transportation Conditions
-
Consider the storage environment, such as temperature, humidity, and exposure to chemicals or moisture.
-
Evaluate the transportation methods and conditions, including the mode of transport, distance, and potential hazards.
-
Choose a pallet material that can withstand the storage and transportation conditions without compromising the integrity of your products.
3. Industry-Specific Requirements
-
Comply with industry-specific regulations and standards, such as ISPM 15 for international shipping or FDA requirements for food and pharmaceutical industries.
-
Consider the specific needs of your industry, such as cleanliness, sterility, or chemical resistance.
4. Material and Durability
-
Evaluate the durability and lifespan of different pallet materials, such as wood, plastic, metal, or corrugated paper.
-
Consider the environmental impact and sustainability of the pallet material.
-
Choose a material that offers the best balance of strength, durability, and cost-effectiveness for your specific application.
5. Compatibility with Handling Equipment
-
Verify the pallet is compatible with your handling equipment, such as forklifts, pallet jacks, or automated systems.
-
Consider the number of entry points (two-way or four-way) required for efficient handling and storage.
Factor | Considerations |
---|---|
Load Weight and Size |
- Product weight and dimensions - Pallet load capacity - Pallet size compatibility |
Storage and Transportation Conditions |
- Temperature, humidity, and exposure - Mode of transport and distance - Pallet material suitability |
Industry-Specific Requirements |
- Regulations and standards - Specific industry needs (cleanliness, sterility, chemical resistance) |
Material and Durability |
- Durability and lifespan of pallet materials - Environmental impact and sustainability - Strength, durability, and cost-effectiveness balance |
Compatibility with Handling Equipment |
- Compatibility with forklifts, pallet jacks, or automated systems - Number of entry points (two-way or four-way) |
By carefully evaluating these factors and consulting with pallet specialists, you can select the most suitable pallet for your specific needs, ensuring the safe and efficient handling of your goods throughout the supply chain.
Conclusion
In closing, wooden pallets are an essential component of modern supply chains, offering a cost-effective and sustainable solution for storing and transporting goods. Fundamental points include:
-
Wooden pallets are made from both hardwoods and softwoods, each with unique advantages.
-
The pallet manufacturing process involves sourcing lumber, cutting and shaping components, and assembling the pallets using various methods. Learn more about different pallet options from Alliance Packing.
-
Wooden pallets can be recycled, repaired, and reused multiple times, contributing to their environmental sustainability.
-
Proper selection of pallets based on factors such as load capacity, storage conditions, and industry requirements is integral for ideal performance.
By understanding the materials, manufacturing process, and environmental impact of wooden pallets, businesses can make informed decisions that fit their operational needs and sustainability goals. Readers are encouraged to investigate the fascinating world of wooden pallets further and discover how these unsung heroes keep global supply chains moving smoothly.